Introduction
Floating offshore wind power enables installations in water depths exceeding 50 m, unlocking Japan’s vast deep-water wind resources and positioning itself as a cornerstone of the nation’s renewable energy strategy. By combining advanced platform stability mechanisms with proven turbine technology, floating systems can achieve annual availability rates above 95 %. In this article, we’ll cover the fundamentals of platform design—balancing static and dynamic stability—and then examine the four principal platform types (semi-submersible, spar, barge, and tension-leg) in detail, highlighting their design considerations, site suitability, and respective advantages and challenges.
While this article dives into a specific topic, we recommend starting with this summary article for a full understanding of floating offshore wind’s key structures and technologies:
👉 The Basics of Floating Offshore Wind: Key Structures and Technologies
This article takes a deep dive into this specific topic, but if you’re looking for a comprehensive overview of offshore wind technologies, check out our full summary article here:
👉 Offshore Wind Technology 2025: Foundations, Floating Wind, Turbines, and Innovations
1. Design Fundamentals: Stability & Dynamic Response
Effective platform design requires a dual focus on static stability—ensuring the center of gravity (CG) remains below the center of buoyancy (CB) to provide a strong righting moment—and dynamic stability, which addresses how the platform responds to waves, wind loads, and currents. Achieving both involves optimizing ballast placement, selecting appropriate mooring systems, and conducting detailed dynamic analyses that account for linear and non-linear responses. These efforts yield platforms that resist excessive motions, protect turbine components, and maintain steady power production under harsh offshore conditions.
1-1. Center of Gravity & Buoyancy Optimization
Ballast, often composed of concrete or high-density materials, is strategically placed to lower the CG relative to the CB. A lower CG increases the metacentric height (GM), enhancing static stability. Designers must also consider draft limits for port assembly and towage, ensuring sufficient underkeel clearance during transport while preserving the stability margin required offshore.
1-2. Mooring Systems
Floating platforms employ either catenary moorings—where chains or lines form a sagging curve to absorb wave and wind forces—or tension-leg moorings (TLP), which use taut tendons to minimize vertical and horizontal motions. Catenary systems offer simpler installation and motion damping but allow greater platform movement. TLP systems provide near-rigid positioning but require precise tendon pretensioning and dynamic load control. Site water depth, wave climate, seabed conditions, and nearby marine traffic inform the optimal mooring choice.
1-3. Dynamic Analysis & Response Prediction
Designers use a combination of linear spectral analysis and non-linear time-domain simulations to predict platform motions under joint wind, wave, and current loading. Standardized design states—such as the 50-year storm wave height and extreme design wind speed per IEC/EN guidelines—form the basis for load cases. Simulation outputs guide adjustments to mooring line length, ballast distribution, and natural period tuning to avoid resonance and ensure fatigue life targets are met.
2. Key Platform Types: Features & Selection Criteria
Four main floating platform concepts dominate the market: semi-submersible, spar, barge, and tension-leg platforms. Each has distinct structural characteristics, water-depth ranges, and deployment requirements. The table below summarizes their key attributes, followed by a deeper dive into site-specific advantages and engineering trade-offs.
Type | Characteristics | Depth Range | Advantages | Challenges |
---|---|---|---|---|
Semi-Submersible | Multiple columns + submerged pontoons for low motion | 50–300 m | Supports large turbines; towable from port to site | Higher fabrication cost; complex assembly |
Spar | Deep-draft cylindrical hull with ballast | >300 m (suitable for thousands of meters) | High stability; proven track record | Requires deep-water installation vessels |
Barge | Flat-bottom hull; simple construction | 50–100 m | Buildable in existing dry docks; no SEP vessel needed | Large motions; needs additional damping solutions |
Tension-Leg Platform (TLP) | Taut tendons for minimal motions | >80 m | High energy yield; small footprint | Complex tendon pretensioning; transient installation loads |
3. Detailed Type Descriptions
3-1. Semi-Submersible
Composed of multiple vertical columns connected by pontoons below the waterline, semi-submersible platforms excel at attenuating wave loads and maintain low motions even in moderate depths (50–300 m). They support turbines of 15 MW and above and can be assembled in sheltered waters before towing to the site, reducing the need for large lifting vessels. The main drawback is the complexity of large-scale fabrication and welded connections, which can drive up initial costs without volume production efficiencies.
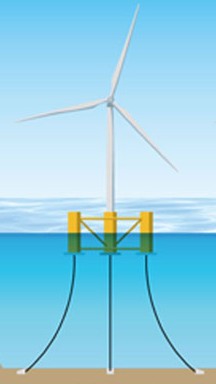
3-2. Spar
Featuring a tall, slender cylindrical hull ballasted at the bottom, spar platforms offer exceptional stability by shifting the center of gravity far below the waterline. They have been successfully deployed in deep waters—most notably by the Hywind Scotland project—and are well-suited for depths of several hundred to thousands of meters. However, their deep draft necessitates specialized deep-sea installation vessels and limits port assembly options.
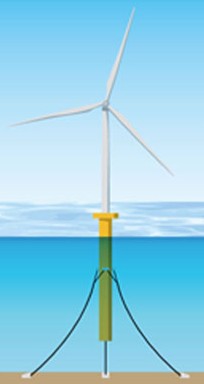
3-3. Barge
Characterized by a broad, flat-bottom hull, barge platforms are straightforward to build in conventional shipyards or dry docks. They are ideal for shallower sites (50–100 m) and can tow fully assembled with the turbine installed, eliminating the need for self-elevating installation vessels. Yet their large water plane area leads to significant heave and pitch motions, requiring supplemental damping devices or tuned mass dampers to maintain operational stability.
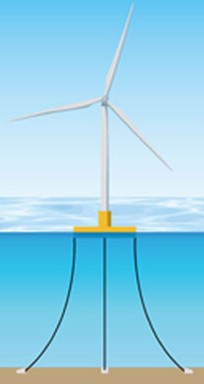
3-4. Tension-Leg Platform (TLP)
TLPs use high-tension tendons anchored to the seabed to virtually eliminate vertical and horizontal motions, maximizing energy yield and reducing fatigue loads on turbine components. Suitable for depths exceeding 80 m, TLPs occupy a small area, minimizing interference with shipping and fishing activities. Installation complexity lies in achieving precise tendon pretensioning and managing transient loads during suction or pile installation of tendons.
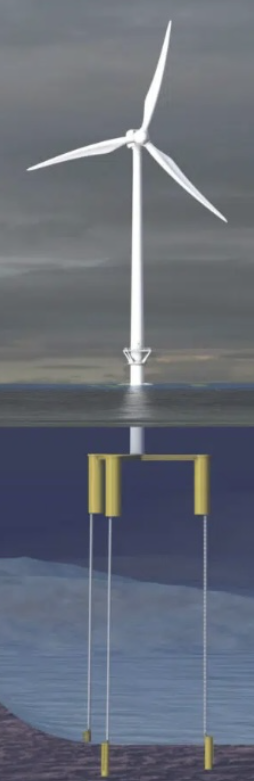
Conclusion & What’s Next
Each floating platform concept brings distinct engineering and logistical trade-offs. Selecting the right design requires a comprehensive assessment of site conditions—water depth, wave climate, port infrastructure, and installation vessel availability. In Part 3, we will explore cost structures, CAPEX/OPEX breakdowns, and LCOE modeling to evaluate the economic competitiveness of floating offshore wind and guide investment decisions.
To further explore the fundamental structures and design concepts of floating offshore wind, check out our in-depth overview here:
🌊 The Basics of Floating Offshore Wind: Key Structures and Technologies
For a broader look at offshore wind technologies and future innovations, make sure to explore our comprehensive summary article:
🌊 Offshore Wind Technology 2025: Foundations, Floating Wind, Turbines, and Innovations
Explore more categories at DeepWind:
- 🔍Market Insights – Understand the latest trends and key topics in Japan’s offshore wind market
- 🏛️Policy & Regulations – Explore Japan’s legal frameworks, auction systems, and designated promotion zones.
- 🌊Projects – Get an overview of offshore wind projects across Japan’s coastal regions.
- 🛠️Technology & Innovation – Discover the latest technologies and innovations shaping Japan’s offshore wind sector.
- 💡Cost Analysis – Dive into Japan-specific LCOE insights and offshore wind cost structures.